Our Services
Injection
Moulding
We specialize in rubber injection moulding using high-quality materials, delivering precision parts for both high and low-volume production.
Compression Moulding
Our compression moulding process shapes natural and synthetic rubbers by compressing pre-heated material in a heated mould cavity.
Transfer
Moulding
We provide transfer moulding, where heated raw rubber is transferred into a mould cavity, allowing it to cure and take shape.
Insert Moulding
Our insert moulding process embeds metal parts into rubber using injection moulding for a wide range of applications.
Rubber Extrusion
We create extruded rubber products by forcing soft, unvulcanized rubber through a die, requiring vulcanization for final usability.
In-House Tooling
At Makarjyothi, we offer in-house tooling as part of our one-stop service, ensuring quality control and efficiency in manufacturing all your parts.
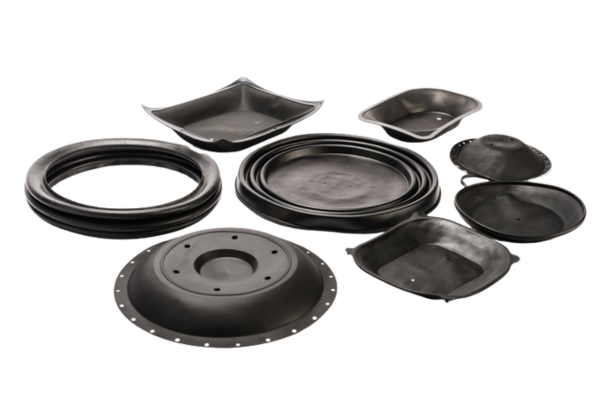
Injection Moulding
We specialize in rubber injection moulding using materials like EPDM, Neoprene, and Silicone, tailored to your needs. Our process simplifies tooling, often without an ejection system. We handle both high and low-volume production, with manual inserts for low-volume parts to reduce parting lines and ejection complexity. Our expertise ensures minimal flashes for high-quality moulded parts.
Compression Moulding
We offer compression moulding, a technique that shapes natural and synthetic rubbers. Pre-heated material is placed in a mould cavity, and two mould halves are compressed under heat and pressure, allowing the material to fill every detail. After cooling, the rubber solidifies into the desired shape with precision.
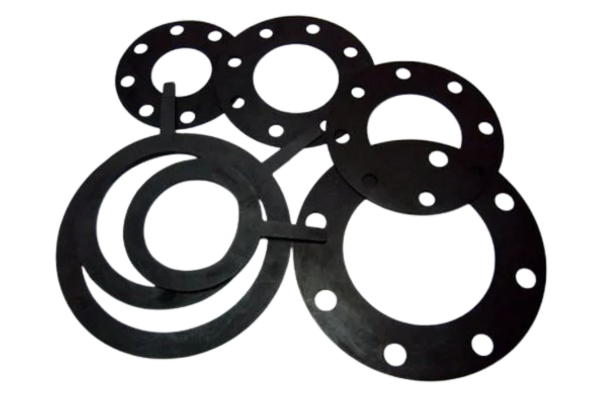
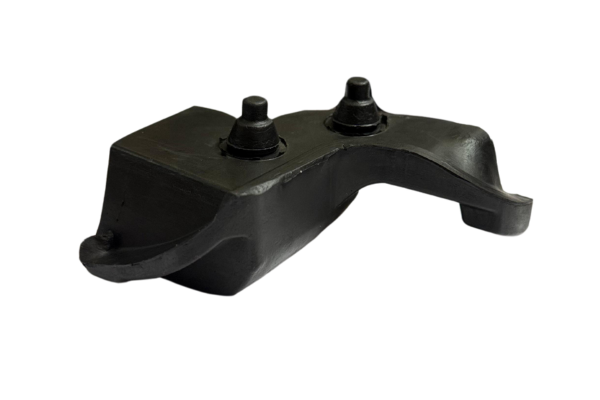
Transfer Moulding
We offer transfer moulding, a process more complex than compression moulding but simpler than injection moulding. In this method, raw rubber is heated in a chamber, then transferred into the mould cavity through a sprue as the press closes. The mould is compressed, allowing the rubber to cure and take its final shape.
Insert Moulding
We offer insert moulding, an injection moulding process that embeds metal parts into rubber to form a final component. The process involves two key steps: preparing and loading the metal insert into the mould, followed by injecting molten rubber into the cavity. Once cooled, the final rubber component is removed. Insert moulding has a wide range of applications.
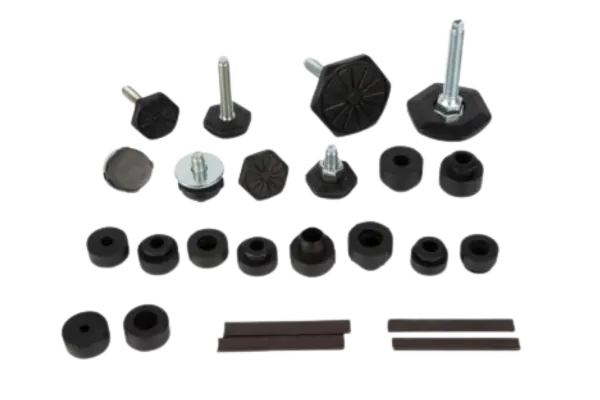
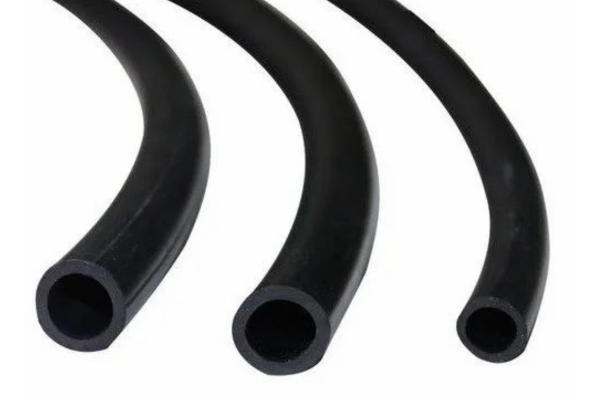
Rubber Extrusion
Extruded rubber products differ from moulded ones in their manufacturing process. Extruded parts are forced through a die of the desired cross-section using an extruder, typically with soft, unvulcanized rubber compounds. After extrusion, the rubber remains soft and pliable, requiring vulcanization or hardening before the products are usable.
In-House Tooling
Tooling requires a significant upfront investment, serving as the foundation for thousands of parts. A single defect can lead to flaws in all parts, and fixing it can be costly. Therefore, manufacturers and designers must choose partners wisely and consider risk mitigation strategies. In-house tooling provides a solution, ensuring quality control from start to finish. At Makarjyothi, we offer a one-stop service with in-house tooling to manufacture all your parts under one roof, ensuring efficiency and precision.
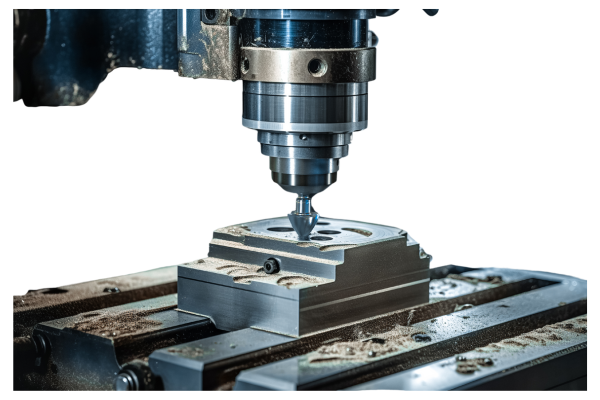